Pressing line
Double discharge one with two automatic silo system, large silo arranged on the top of the mixer, hence the name top silo. Good sealing, little dust, high efficiency and no pollution. The system is mainly composed of silo, weighing tank, pipeline, set hopper, sub-hopper, etc. The compact connection between the equipment and the perfect combination of mixing system. The system adopts PLC control, man-machine interface is easy to operate. The weighing device adopts a high-precision weighing system to ensure that the formula ratio fluctuates within the allowable range. It consists of four subsystems: sand system, powder system, resin system and dust removal system.
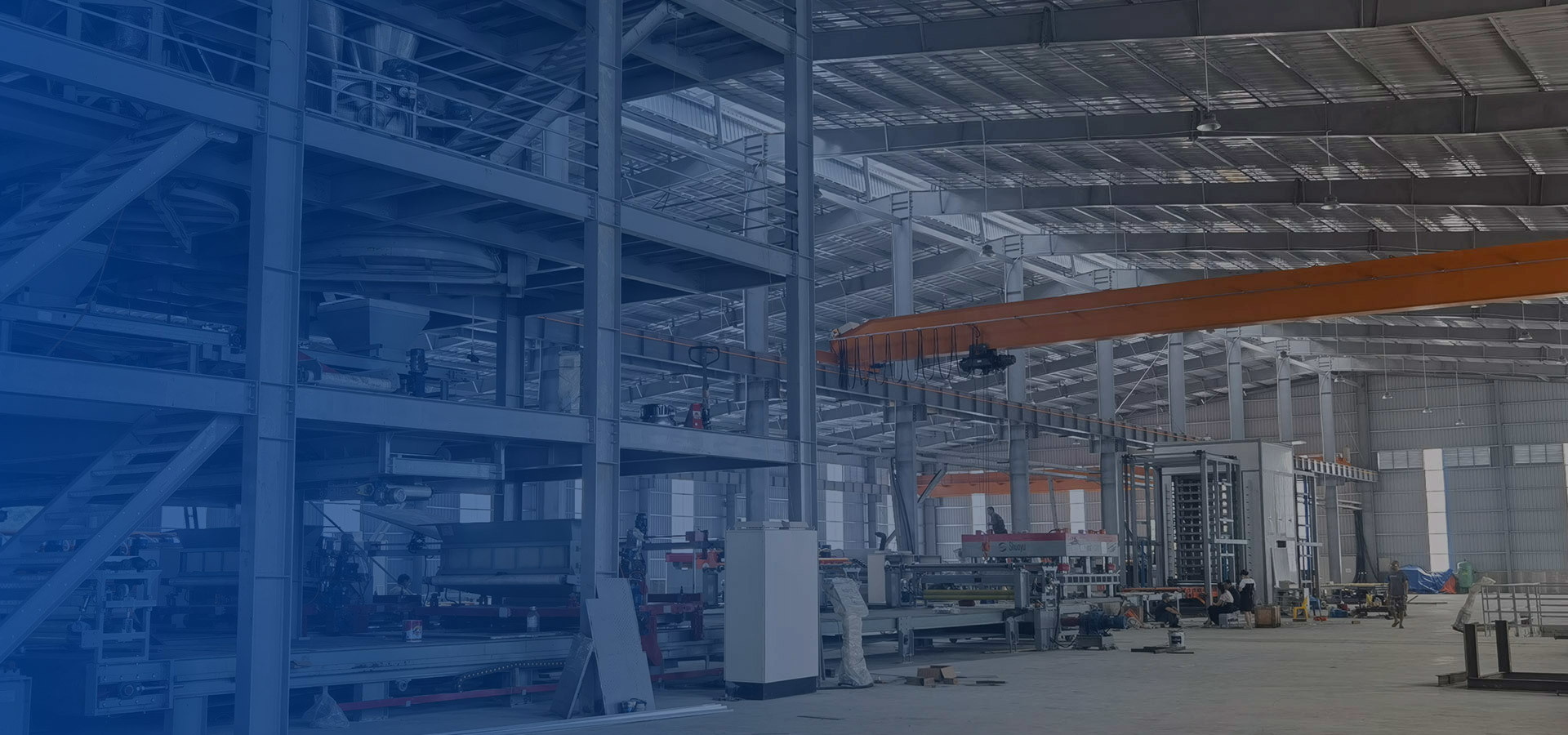
Pressing line
Overall System Overview
Double discharge one with two automatic silo system, large silo arranged on the top of the mixer, hence the name top silo. Good sealing, little dust, high efficiency and no pollution. The system is mainly composed of silo, weighing tank, pipeline, set hopper, sub-hopper, etc. The compact connection between the equipment and the perfect combination of mixing system. The system adopts PLC control, man-machine interface is easy to operate. The weighing device adopts a high-precision weighing system to ensure that the formula ratio fluctuates within the allowable range. It consists of four subsystems: sand system, powder system, resin system and dust removal system.
Sand material system
The large sand bin is a double-outlet silo equipped with two belt guides. The belt guides of the two large sand bins share a weighing hopper with one length and one short. The storage hoppers are staggered and arranged on the following two large sand conveyor belts. The two large sand conveyor belts are transported in opposite directions, left and right, and are respectively transported to the mixers of the two pressing plate lines.
The belt guide under the sand bin is started and stopped under the control of the weight of the weighing hopper. After the weighing hopper is in place according to the program, multiple weighing hoppers open the valve to put the material into the collection hopper. A storage hopper delivered by a rotating sub-hopper to a designated mixer.
Powder system
The large powder bin can have 1-3 outlets, each outlet is equipped with a screw conveyor, and each screw conveyor is equipped with a weighing storage hopper. Two pressure plate lines are respectively configured with a set of mechanical parts of the system
The screw conveyor is started and stopped by the weight control of the weighing hopper. After the weighing hopper is in place according to the program, the valve is automatically selected to open the machine to put the powder into the mixer of the pressing plate line.
Resin System
The resin system consists of a large resin mixing tank, pipelines, color slurry disperser and valves.
Each color paste dispersing machine has a weighing small barrel, the large resin barrel flows to the weighing small barrel through the pipeline, and the weighing small barrel passes through the weighing control valve. Additives such as quantitative color paste and curing agent added to the weighing keg are manual operations. After the mixing of resin, color paste and additives is completed, oil valves are installed at both ends of the hose connected to the mixer, and the system automatically opens the valves to flow resin into the mixer barrel. Each press plate line mixer is equipped with a color paste dispersing machine.
Dust removal system
The main machine of the dust removal system is configured according to the actual situation of the workshop. It can be considered that the silo system, the mixing part and the pressing plate part share one main machine.
The dust removal of the silo system is divided by the main air pipe and the dust removal port, and each dust removal port is equipped with a manual valve.
Related Products